High-Detail 3D Scans for VR Training of Engine Runs
At JetSupport, we continuously invest in technologies that strengthen the efficiency and quality of our maintenance processes. A recent innovation is the integration of 3D scanning technology to support VR-based engine run training for the Dassault Falcon 2000. By digitizing the cockpit in high detail, we aim to elevate the training experience for our technicians and increase the realism and effectiveness of Virtual Reality scenarios.
From Photo to Scan: A Leap in Accuracy
The initial VR model of the Falcon 2000 cockpit was developed using manually processed photographs. Thanks to the skill of the model developer, this method already delivered a highly photorealistic and dimensionally accurate result. However, the process of selecting and processing the photos was time-consuming and labor-intensive.
To speed up the workflow and further improve consistency and scalability, we’ve recently implemented full 3D scans of the cockpit. The output shows a high level of detail in form, dimensions, and texture. For example, the 3D rendering of a cockpit seat accurately replicates the fabric texture and shape — making the simulation more intuitive and immersive for training purposes.
Optimization and Standardization to Scalable Practice
We are currently analyzing how the scanned 3D data can best be integrated with our existing VR training platform. Early results are promising: using these scans, we’re able to further optimize the Falcon 2000 model for training applications. The goal is to provide our technicians with a highly realistic and user-friendly VR cockpit environment for engine run procedures.
If this approach proves successful, JetSupport will deploy this technology as standard for future aircraft types. This aligns with our commitment to High Quality Aircraft Maintenance and innovative training methods that contribute to Aircraft Availability Solutions.
Practical Application: Faster and Better Training
For JetSupport customers, this concretely means their aircraft are maintained by technicians trained in a virtual environment that is nearly indistinguishable from reality. This accelerates the learning effect, reduces the chance of errors, and increases overall safety during engine runs.
Thanks to this innovation, we can better align our services with the needs of operators including Dassault Falcon Maintenance aircraft. The VR platform is fully integrated within our training programs at locations such as JetSupport Amsterdam and our stations in Paris, Munich, and Nice.
Future-Oriented Technology as Part of Reliable Support
At JetSupport, we believe that future-oriented technologies go hand in hand with reliable, personal service. The 3D scanning of cockpit interiors is a logical continuation of our existing services, such as Scheduled Aircraft Maintenance, Avionics Upgrades for Business Jets, and Aircraft Interior Refurbishment.
By taking this step, we strengthen our position as a leading European MRO for Business Aviation, with a strong focus on continuous improvement and customer-oriented solutions.
Want to Know More?
Would you like to know how we deploy this innovative technology for your fleet? Or are you curious about our capabilities for Business Jet Maintenance and VR-based training for your maintenance team? Contact our team or discover our hangar at Schiphol.
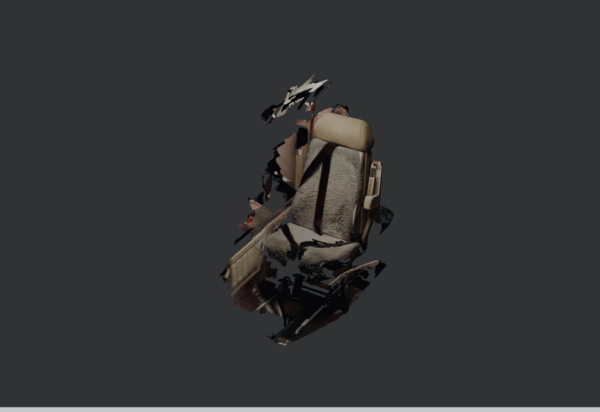